在工业领域,氮气因其惰性、无腐蚀性、化学性质稳定等特性,在化工、电子、食品、医药等众多行业有着极为广泛的应用。当下,深冷空分制氮、变压吸附(PSA)制氮和膜分离制氮已成为主流的制氮方法。本文将从原理、特点、适用场景等多维度对这三种技术展开深入且专业的对比分析。
深冷空分制氮、PSA变压吸附制氮和膜分离制氮是工业制氮的三种主流技术。深冷空分技术适用于大流量、高纯度的氮气需求,设备复杂且能耗较高,适合石油化工、钢铁等行业。PSA技术则具有启动快、成本低的优势,适合中小规模应用,尤其在电子制造、食品保鲜等领域。膜分离制氮响应速度快、结构简单,适合对纯度要求较低的行业,如油田注氮和激光切割。
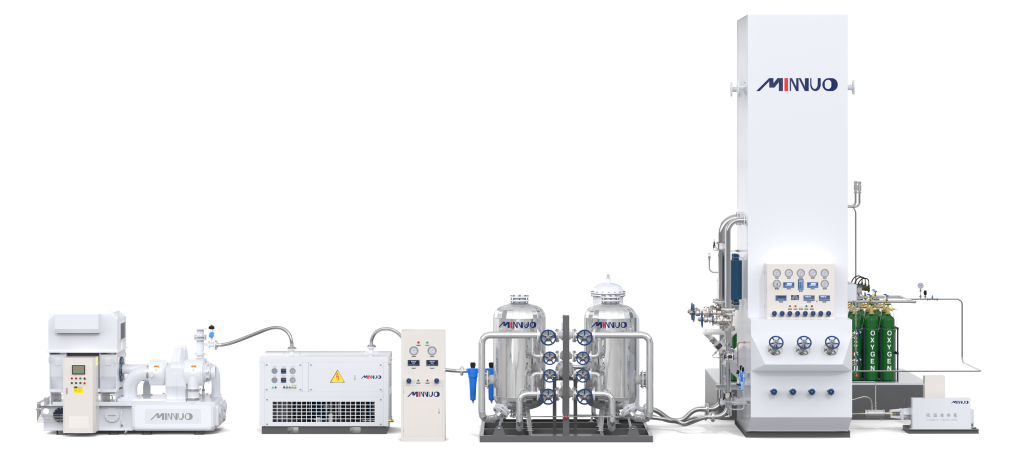
一、深冷空分制氮
(1)原理与流程
深冷空分制氮作为一种传统且经典的工艺,已有长达数十年的发展历程。其核心原理基于空气各组分沸点的显著差异,通过深度冷冻的方式实现空气的分离。具体流程如下:
- 空气压缩:外界空气首先进入空气压缩机,在压缩机的作用下,空气压力被提升至 0.6 – 0.8MPa,这一过程不仅为后续的净化和冷却提供动力,还能使空气的物理性质更便于处理。
- 空气净化:压缩后的空气含有水分、二氧化碳、碳氢化合物等杂质,这些杂质若不除去,会在后续的低温过程中结冰或堵塞管道,影响设备正常运行。因此,压缩空气需依次通过空气预冷系统、分子筛纯化系统进行净化。在空气预冷系统中,利用冷冻水或循环水将压缩空气冷却至 10 – 15℃,使大部分水蒸气冷凝成液态水分离出去;分子筛纯化系统则采用特制的分子筛吸附剂,进一步吸附残留的水分、二氧化碳和碳氢化合物,确保净化后的空气露点达到 – 65℃以下,二氧化碳含量低于 1×10⁻⁶。
- 空气液化:净化后的空气进入主热交换器,与返流的低温气体进行热交换,逐步被冷却至接近液化温度(约 – 196℃)。随后,经过节流阀节流降压,使空气进一步降温并液化,形成液态空气(液空)。
- 精馏分离:液空进入精馏塔,精馏塔通常由上塔和下塔组成。在下塔中,液空在一定压力下进行初步精馏,由于氧的沸点( – 183℃)高于氮的沸点( – 196℃),沸点较高的氧逐渐富集在塔底,形成富氧液空;沸点较低的氮则在塔顶以气态形式逸出,经过冷凝后一部分作为液氮产品输出,另一部分作为回流液返回下塔,以保证精馏过程的传质传热。富氧液空经节流阀进入上塔,继续进行精馏,最终在塔顶得到高纯度氮气(纯度可达 99.999%),在塔底得到高纯度液氧。
(2)技术特点
- 高纯度与大产能:深冷空分制氮技术能够稳定生产超高纯度氮气,纯度通常可达 99.999% 以上,甚至在一些先进的装置中,氮气纯度可达到 99.9999%。单机产能方面,大型深冷空分制氮设备的产能可达数千至数万 Nm³/h,例如某大型钢铁企业使用的深冷空分制氮装置,单机产能可达 50000Nm³/h,完全能够满足大规模工业生产对高纯度、大流量氮气的需求。
- 设备复杂:深冷空分制氮设备是一个庞大而复杂的系统,需配备大型空气压缩机、空气预冷系统、分子筛纯化系统、主热交换器、精馏塔等一系列关键设备。整个装置占地面积大,以一套产能为 10000Nm³/h 的深冷空分制氮设备为例,其占地面积通常在 2000 – 3000 平方米左右。建设成本高昂,不仅设备采购费用高,还涉及到复杂的安装调试工程,建设周期较长,一般需要 1 – 2 年时间。
- 运行成本与启动时间:深冷空分制氮设备能耗较高,主要原因在于空气的压缩和低温制冷过程需要消耗大量电能。据统计,生产 1Nm³ 纯度为 99.999% 的氮气,能耗约为 0.6 – 0.8kWh。启动时间长超6小时,这是因为在启动过程中,需要逐步将设备各系统冷却至低温状态,建立稳定的精馏工况,期间涉及到设备的预热、预冷、调试等多个环节,任何一个环节出现问题都可能导致启动时间延长。因此,深冷空分制氮设备适合连续稳定运行的大规模工业场景,频繁启停会极大地增加运行成本和设备损耗。注:
- 小型深冷空分设备:如 KZO-120 型制氧机,流量为 120Nm³/h,启动时间一般在 6-8 小时。
- 中型深冷空分设备:常见的 6000m³/h 空分设备,正常开车启动时间可能在 10 小时以上,如果进行优化操作可缩短 3 小时左右。
- 大型深冷空分设备:像 35000m³/h 及以上的大型空分设备,启动过程更为复杂,启动时间可能需要 24 小时甚至更长。
- 经济性:对于 3500Nm³/h 以下的产能需求,深冷制氮的投资成本比 PSA 制氮高 20% – 50%。这是因为深冷空分制氮设备的复杂性和大型化,使得设备采购、安装调试、维护保养等成本都远高于 PSA 制氮设备。然而,在大规模制氮需求(产能大于 3500Nm³/h)下,随着产量的增加,深冷空分制氮的单位成本逐渐降低,显示出其规模经济优势,更适用于超大规模制氮需求。
(3)适用场景
深冷空分制氮技术适用于石油化工、钢铁冶金、煤化工等需要高纯度、大流量氮气的行业。在石油化工行业,氮气常用于加氢裂化、催化重整等工艺过程中的保护气、置换气和吹扫气,要求氮气纯度高且流量稳定;钢铁冶金行业中,在转炉炼钢、连铸连轧等环节,高纯度氮气用于氧枪的冷却、钢水的保护浇注等,对氮气的纯度和流量要求也极为严格。例如,在某大型石油化工企业的加氢裂化装置中,使用深冷空分制氮设备提供纯度为 99.999%、流量为 8000Nm³/h 的氮气,确保了加氢裂化反应的安全稳定进行。
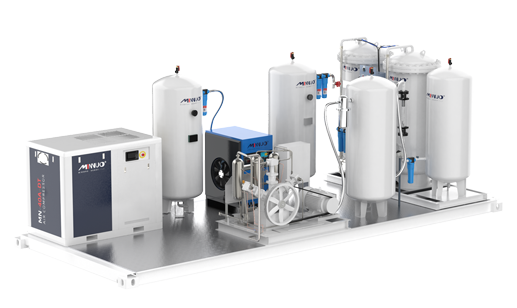
二、PSA 变压吸附制氮
(1)原理与流程
PSA(Pressure Swing Adsorption)制氮技术兴起于 20 世纪 70 年代,是一种基于吸附剂对不同气体吸附特性差异的气体分离技术。其核心是利用碳分子筛对氧气和氮气的选择性吸附实现分离。具体流程如下:
- 空气压缩:外界空气通过空气压缩机压缩至 0.7 – 0.8MPa,为后续的吸附分离提供动力。
- 空气净化:压缩后的空气同样含有水分、油分和杂质,需先经过空气过滤器去除大部分液态水和固体杂质,再通过冷冻式干燥机将空气露点降至 2 – 10℃,进一步除去水分,以保证后续吸附过程的正常进行。
- 吸附分离:净化后的空气进入吸附塔,塔内装填有碳分子筛吸附剂。在加压条件下(通常为 0.7 – 0.8MPa),碳分子筛对氧气、二氧化碳和水蒸气等具有较强的吸附能力,而对氮气的吸附能力较弱。因此,氧气、二氧化碳和水蒸气被碳分子筛优先吸附,氮气则直接通过吸附床层,作为产品气被收集。当碳分子筛吸附达到饱和状态时,通过降低吸附塔内压力(通常降至常压),使被吸附的氧气、二氧化碳和水蒸气解吸出来,实现吸附剂的再生。通过多个吸附塔的交替工作,即可实现连续产氮。
(2)技术特点
- 灵活性与便捷性:PSA 制氮设备启动时间短,一般仅需 15 – 30 分钟即可达到稳定产氮状态,能够快速响应生产需求的变化。氮气纯度可在 95% – 99.999% 范围内灵活调节,通过调整吸附时间、吸附压力等操作参数,即可满足不同用户对氮气纯度的要求。设备自动化程度高,采用先进的可编程逻辑控制器(PLC)控制系统,可实现远程监控和自动调节,大大降低了人工操作强度和劳动成本。
- 成本优势:设备结构紧凑,占地面积小,一套产能为 1000Nm³/h 的 PSA 制氮设备,占地面积通常在 50 – 100 平方米左右。投资成本低于深冷空分制氮设备,主要原因在于其设备相对简单,无需复杂的低温制冷系统和大型精馏塔。运行成本方面,由于无需消耗大量电能用于制冷,其能耗相对较低,生产 1Nm³ 纯度为 99% 的氮气,能耗约为 0.3 – 0.5kWh。尤其适合中小规模需求(200 – 3000Nm³/h),在该产能范围内,PSA 制氮设备的性价比优势明显。
- 维护简便:PSA 制氮设备无低温设备,主要设备为吸附塔、空气压缩机、空气净化设备等,设备结构和工作原理相对简单。吸附剂碳分子筛的使用寿命一般为 5 – 8 年,期间只需定期对空气过滤器、干燥机等设备进行维护保养,更换易损件,维护频率低,操作门槛较低,普通技术人员经过简单培训即可熟练操作和维护。
- 能耗:相比深冷技术,PSA 制氮能耗更低。但需要注意的是,当氮气纯度超过 99.9% 时,为了保证较高的纯度,需要延长吸附时间或增加吸附塔的数量,这会导致能耗显著增加。例如,将氮气纯度从 99% 提高到 99.99%,能耗可能会增加 30% – 50%。
(3)适用场景
PSA 制氮技术适用于电子元器件制造、食品保鲜、医药包装等中小规模且对纯度要求多样的行业。在电子元器件制造行业,如芯片制造过程中,需要使用高纯度氮气对芯片进行吹扫和保护,防止芯片在制造过程中被氧化或污染,根据不同的工艺要求,氮气纯度可在 99.9% – 99.999% 之间选择;食品保鲜行业中,利用氮气的惰性,将其充入食品包装中,置换出包装内的氧气,延长食品的保质期,一般要求氮气纯度在 95% – 99% 之间;医药包装行业,氮气用于药品包装的保护气,防止药品氧化变质,对氮气纯度的要求也较为灵活。例如,某电子芯片制造企业使用 PSA 制氮设备,根据不同的芯片制造工艺,提供纯度为 99.99% – 99.999% 的氮气,满足了生产过程中对氮气纯度和流量的需求。
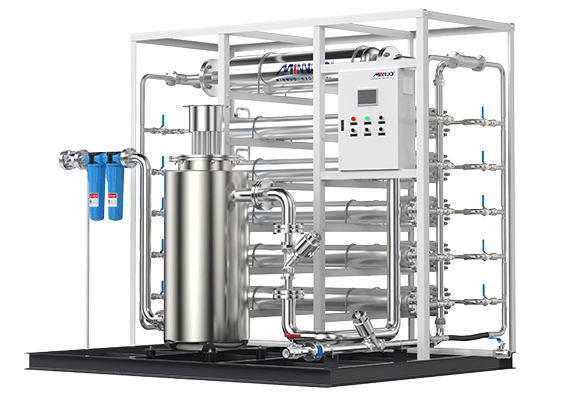
三、膜分离制氮
(1)原理与流程
膜分离制氮技术是一种基于气体组分在高分子膜中渗透速率差异的新型气体分离技术。其原理是利用特殊的高分子膜材料,对不同气体具有不同的渗透选择性。氧气、水蒸气等 “快气” 分子透过膜壁的速度快于氮气,剩余气体则以富氮形式输出。具体流程如下:
- 空气压缩:外界空气经空气压缩机压缩至 0.7 – 1.0MPa,提高空气的压力,为气体透过膜组件提供动力。
- 空气净化:压缩后的空气同样需要进行净化处理,先通过空气过滤器去除空气中的灰尘、杂质和液态水,再通过活性炭过滤器去除异味和残留的油分,以保证进入膜组件的空气清洁,避免膜组件被污染和堵塞。
- 膜分离:净化后的空气进入膜组件,膜组件由成千上万根中空纤维膜组成,每根中空纤维膜的内径一般在 0.05 – 0.2mm 之间。当空气在压力作用下进入膜组件时,氧气、水蒸气等 “快气” 分子由于其较小的分子尺寸和较高的扩散系数,能够快速透过膜壁进入膜的另一侧,而氮气分子则大部分被截留,从而在膜的出口端得到富氮气体。通过调整膜组件的数量和操作压力,可以控制氮气的纯度和流量。
(2)技术特点
- 极速响应:膜分离制氮设备启动时间仅需 3 分钟左右,几乎可以实现瞬间供氮,这是其区别于其他两种制氮技术的显著优势之一。这种极速响应能力使其特别适合频繁启停或应急供氮场景,如油田注氮作业中,当需要临时增加注氮量或应对突发情况时,膜分离制氮设备能够迅速启动并提供所需氮气。
- 结构简单:膜分离制氮设备无阀门切换或复杂控制系统,主要由空气压缩机、空气净化设备和膜组件组成,设备体积小,结构紧凑。一套产能为 50Nm³/h 的膜分离制氮设备,占地面积通常在 10 – 20 平方米左右,便于安装和移动。维护成本极低,膜组件的使用寿命一般为 3 – 5 年,期间只需定期对空气过滤器、活性炭过滤器等进行简单维护,无需专业技术人员进行复杂的维护操作。
- 纯度限制:膜分离制氮技术的经济纯度范围在 95% – 98% 之间。若需 99% 以上纯度的氮气,需要采用多级膜分离或与其他技术相结合的方式,这会导致设备成本大幅增加,比 PSA 制氮机高出 15% 以上。这是因为随着氮气纯度的提高,膜组件的数量和性能要求也相应提高(Air products,Generon等品牌的单个膜组可以达到99.5%),同时还需要增加辅助设备来实现更精细的气体分离。
- 扩展性:膜分离制氮设备可通过并联膜组件快速扩容,根据生产需求的变化,只需增加膜组件的数量,即可方便地提高设备的产能。这种良好的扩展性使其适合动态需求的场景,如小型实验室随着实验项目的增加,对氮气的需求量也会相应增加,通过并联膜组件即可轻松实现设备的扩容。
(3)适用场景
膜分离制氮技术适用于油田注氮、激光切割、小型实验室等对纯度要求中等(≤98%)、需快速供氮的领域。在油田注氮作业中,氮气用于提高原油采收率,对氮气的纯度要求一般在 95% – 98% 之间,膜分离制氮设备能够快速响应油田注氮的需求,及时提供所需氮气;激光切割行业中,氮气作为辅助气体,用于吹除切割过程中产生的熔渣和防止切割面氧化,对氮气纯度要求不高,一般在 95% 左右,膜分离制氮设备的快速供氮和低成本优势使其在该领域得到广泛应用;小型实验室在进行一些常规实验时,对氮气的需求量不大,但要求能够快速获得氮气,膜分离制氮设备正好满足这一需求。例如,某油田使用膜分离制氮设备,为注氮作业提供纯度为 97% 的氮气,设备能够在短时间内启动并稳定运行,满足了油田对氮气的快速供应需求。
四、综合对比与选型建议
技术指标 | 深冷空分制氮 | PSA 制氮 | 膜分离制氮 |
氮气纯度 | 99.999% 以上 | 95% – 99.999% | 95-99.5% |
启动时间 | 12 – 24 小时 | 15 – 30 分钟 | 3 分钟 |
单机产能 | 大规模(>3000Nm³/h)(最小50方也能制造) | 中小规模(200 – 3000Nm³/h)(1-3000立方都能满足) | 小型(<200Nm³/h)(1立方-5000立方都可以制造) |
投资成本 | 高 | 中等 | 低(纯度≤98% 时) |
运行成本 | 高(能耗高) | 低(纯度>99.9% 时能耗增加) | 中等 |
设备复杂度 | 复杂,含大型压缩、制冷、精馏设备 | 较简单,主要为吸附塔和净化设备 | 简单,主要为膜组件和净化设备 |
维护难度 | 高,需专业技术人员维护低温设备 | 低,普通技术人员可维护 | 极低,简单维护膜组件和净化设备 |
适用场景 | 钢铁、化工等重工业,对纯度和流量要求极高 | 电子、食品、医药等中小规模且纯度要求多样的行业 | 油田、激光切割、小型实验室等对纯度要求中等、需快速供氮的领域 |
选型建议
- 超大规模高纯度需求:当企业对氮气的需求量超过 3500Nm³/h,且对氮气纯度要求极高(99.999% 以上)时,优先选择深冷空分制氮技术。虽然其投资成本和运行成本较高,但在大规模生产下,单位成本具有优势,且能够稳定提供高纯度氮气,满足钢铁、化工等重工业的生产需求。
- 中小规模灵活需求:对于产能在 5-3000Nm³/h 之间,且对氮气纯度要求在 95% – 99.999% 范围内灵活变化的企业,PSA 制氮技术性价比最高。其启动时间短、设备成本低、操作维护简便等特点,使其能够很好地适应电子、食品、医药等行业的生产需求。
- 快速响应与中等纯度:如果企业对氮气的需求具有快速响应的特点,且对氮气纯度要求在 95% – 98%(95-99.5%) 之间,如油田注氮、激光切割、小型实验室等领域,膜分离制氮技术是理想选择。但需注意其纯度上限,当对纯度要求超过99.5%时,应综合考虑成本和技术可行性,选择其他更合适的制氮技术。
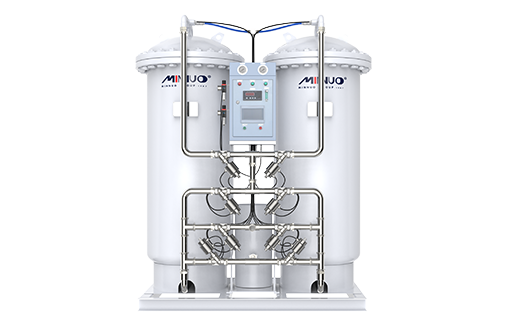
五、MINNUO优势
作为深耕工业制氮领域多年的专业厂商,MINNUO始终以技术创新为核心驱动力,针对不同行业客户的个性化需求,提供高效、可靠、智能化的制氮解决方案。凭借对三大制氮技术的深度研发与集成优化能力,MINNUO在技术适配性、系统能效比及全生命周期服务方面展现出显著优势。基于对垂直领域的深度理解,MINNUO开发行业专属制氮系统:
- 电子级超高纯氮:采用三级催化净化+低温吸附技术,将烃类杂质控制在0.1ppb以下,满足28nm以下芯片制造要求;
- 食品医药级无菌氮:集成过氧化氢灭菌模块与在线微粒监测(0.01μm分辨率),符合FDA 21 CFR Part 11规范;
- 油田注氮增强系统:研发抗脉动膜分离技术,输出压力波动≤±1%,配合井下温压传感器实现注氮精准闭环控制。
六、总结
深冷空分、PSA 和膜分离制氮技术各有其独特的优势和适用范围,它们在不同的工业领域中发挥着重要作用,适用场景相互补充。企业在选型时,必须综合考虑氮气纯度、产能、投资成本、运行成本、维护难度及动态需求。
如果您有任何疑问,欢迎前来MINNUO咨询!