在工业制氮领域,膜分离制氮机因其结构简单、操作便捷、能耗较低等优势被广泛应用。然而,设备运行过程中若出现高温状态,可能对核心部件(如膜组)造成不可逆损伤,甚至影响氮气生产效率。以下从膜分离制氮机的工作原理出发,结合其温控系统特点,分析高温成因并提出针对性解决方案。
膜分离制氮机出现高温的原因主要包括环境温度过高、气流系统异常、温控系统故障、加热器功率异常以及膜组老化或污染,这些因素会导致设备散热不畅或过度发热,影响氮气生产效率。针对这些问题,可采取改善通风环境、清理管道滤网、定期检查温控元件、优化加热器功率配置及定期维护膜组等措施,以确保设备稳定运行并延长使用寿命。
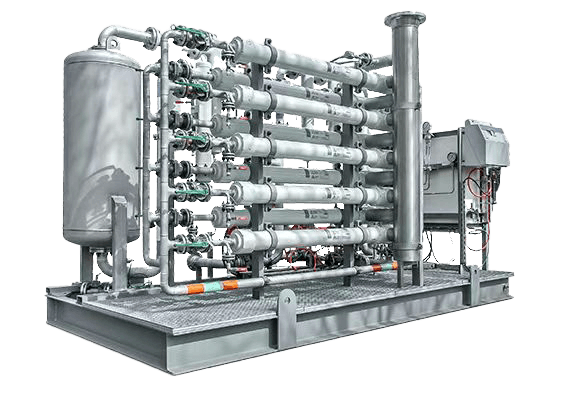
一、膜分离制氮机温控系统原理
膜分离制氮机的核心工作机制是利用中空纤维膜对压缩空气中的氧气和氮气进行选择性渗透,从而实现氮气的高效分离。在这一过程中,温度的精准控制对于确保膜的性能稳定以及整个分离过程的高效运行起着关键作用。其温度控制系统主要由以下几个重要组件协同工作:
(一)热电偶与 PID 温控仪
热电偶作为温度检测的关键元件,能够实时感知设备内部的温度变化,并将温度信号转化为电信号输出。而 PID 温控仪则接收来自热电偶的信号,通过先进的比例(P)、积分(I)、微分(D)算法,对温度信号进行精确处理和分析。然后,PID 温控仪根据预设的温度值和实际测量值的偏差,以时间比例输出的方式来精确控制固态继电器(SSR)的开合状态,进而调节加热器的功率大小。这种闭环控制方式能够快速、准确地对温度进行调节,使设备内部温度始终保持在设定的范围内,确保膜分离过程在适宜的温度条件下进行。
(二)过热保护装置
为了防止设备在运行过程中出现异常高温,膜分离制氮机配备了过热保护装置。当设备内部温度升高到≥50℃时,过热保护装置会迅速自动切断电源,使加热器停止工作,从而避免设备因温度过高而受到损坏。当温度下降到≤35℃时,过热保护装置又会自动恢复供电,加热器重新开始工作,以维持设备的正常运行温度。这种过热保护机制为设备提供了一层可靠的安全保障,有效防止了因温控系统故障或其他原因导致的温度失控情况。
(三)压力联动保护
压力联动保护机制是膜分离制氮机温控系统的又一重要组成部分。当气压达到≥0.4MPa 时,压力开关会自动闭合,此时加热器启动开始工作。这一设计的目的是为了避免在无气流通过的情况下,加热器空烧,从而引发设备过热甚至损坏。只有在有足够气流通过的情况下,加热器才会工作,确保了设备运行的安全性和稳定性。
二、高温状态的常见原因
(一)环境温度过高
制氮机安装环境通风不良或靠近热源:
如果膜分离制氮机安装在通风不畅的狭小空间内,或者周围存在高温热源,如锅炉房、高温炉窑等,设备散发的热量无法及时有效地排出到周围环境中,就会导致散热效率急剧下降。设备内部的热量不断积聚,最终使得设备外壳温度持续上升。这种情况在夏季高温时段尤为容易发生,因为夏季环境温度本身就较高,加上通风不良和热源的影响,设备散热面临更大的挑战。
表现:
设备外壳温度明显升高,用手触摸会感觉到烫手。同时,设备运行的噪音可能会有所增大,这是因为高温导致设备内部的一些部件膨胀或变形,从而引起机械摩擦增加。此外,设备的运行稳定性也会受到影响,可能出现氮气纯度波动等情况。
(二)气流系统异常
空压机供气不足或管路堵塞(如过滤器积碳):
空压机是为膜分离制氮机提供压缩空气的关键设备。如果空压机出现故障,如活塞磨损、密封件老化等,导致供气压力不足,无法满足膜分离过程对气流的需求,就会使气流循环不畅。此外,管路中的过滤器如果长期未进行清洗或更换,积累了大量的灰尘、油污和积碳等杂质,就会造成管路堵塞,阻碍气流的正常流通。这样一来,设备内部产生的热量无法通过气流及时带出,从而导致热量在设备内部积聚,引发高温问题。
表现:
气压波动明显,通过气压表可以观察到气压数值不稳定,忽高忽低。加热器会频繁启停,这是因为当气压不足时,为了维持设备内部的温度和压力平衡,加热器会不断尝试工作来弥补热量的不足,但由于气流不畅,热量又无法有效散发,导致温度很快又升高,从而使加热器频繁启停。同时,设备的氮气产量可能会下降,氮气纯度也会受到影响。
(三)温控系统故障
热电偶老化或信号传输异常:
热电偶长期在高温环境下工作,其内部的金属丝可能会出现氧化、腐蚀等现象,导致热电偶老化,测量精度下降。此外,热电偶与 PID 温控仪之间的信号传输线路如果存在破损、接触不良等问题,也会导致信号传输异常,使 PID 温控仪接收到的温度信号不准确。
PID 参数失调:
PID 温控仪的参数设置对于温度控制的精度和稳定性至关重要。如果在设备调试过程中,PID 参数设置不合理,或者在设备运行过程中,由于外部干扰等原因导致 PID 参数发生变化,就会使温控仪的控制效果变差。例如,比例带设置过大,会导致温控仪对温度变化的响应迟钝;积分时间设置过长,会使系统的调节速度变慢,无法及时消除温度偏差;微分时间设置不当,则可能会导致系统出现振荡,温度波动较大。
SSR 继电器粘连失效:
固态继电器(SSR)在温控系统中起着控制加热器电源通断的作用。如果 SSR 继电器长期频繁工作,或者受到过电压、过电流等因素的影响,其内部的触点可能会出现粘连现象,导致继电器无法正常断开,加热器会持续工作,从而使设备温度不断上升。
表现:
温控仪显示值与实际温度偏差较大,可能会出现显示温度远高于或低于实际温度的情况。加热器不受控持续工作,即使设备内部温度已经超过了设定的上限,加热器仍然不会停止工作。此外,设备的温度波动会变得异常剧烈,无法稳定在设定的温度范围内。
(四)加热器功率异常
加热元件局部短路或功率配置过高:
加热元件在长期使用过程中,可能会由于绝缘层损坏等原因导致局部短路。当加热元件局部短路时,短路部位的电阻会变小,电流会增大,从而使该部位的发热量急剧增加。此外,如果在设备选型或安装过程中,加热器的功率配置过高,超出了设备散热系统的承载能力,也会导致设备在运行过程中产生过多的热量,无法及时散发出去,进而引发高温问题。
表现:
在短时间内,设备内部温度会急剧上升,温度上升速度明显超过正常情况。过热保护装置可能会频繁触发,以防止设备因温度过高而损坏。同时,可能会闻到一股烧焦的气味,这是由于加热元件局部短路导致绝缘材料受热分解产生的。
(五)膜组老化或污染
膜组因高分子材料老化导致气体选择性渗透性能衰减:
膜分离制氮机的膜组在长期使用过程中,会受到压缩空气中的杂质、水分、油污等物质的侵蚀,以及温度、压力等因素的影响,导致膜的性能逐渐下降。其中,膜的渗透性下降是膜组老化的一个重要表现。当膜的渗透性下降时,气体通过膜的阻力增大,为了达到相同的氮气产量,设备需要消耗更多的能量,从而使系统负荷增加,产生更多的热量。
膜组污染:
压缩空气中的灰尘、油污、微生物等杂质会逐渐在膜组表面和内部堆积,形成污垢,这就是膜组污染。膜组污染会进一步降低膜的分离效率,使气体分离过程变得更加困难,系统需要消耗更多的能量来维持运行,进而导致设备温度升高。当压缩空气含油量>0.01ppm、颗粒物>1μm时,悬浮物会通过以下途径影响膜组性能:
- 物理堵塞:颗粒物在膜表面形成滤饼层,阻碍气体渗透;
- 化学吸附:油雾中的烃类物质与膜材料发生溶胀反应;
- 生物滋生:湿度>60%时,微生物在膜内繁殖导致生物污堵。
表现:
氮气纯度下降,无法满足生产工艺对氮气纯度的要求。设备运行噪音增大,这是因为膜组性能下降后,气体在通过膜组时会产生更大的阻力,从而引起设备内部的气流紊乱,导致噪音增大。此外,设备的能耗也会明显增加,生产单位体积氮气所消耗的电量会上升。
故障类型 | 典型表现 | 直接后果 |
膜组老化 | 氮气纯度下降≥5%,能耗上升20%~30% | 生产工艺不达标,成本增加 |
温控系统失效 | 温度波动>±5℃,加热器持续工作 | 膜组热损伤,寿命缩短50% |
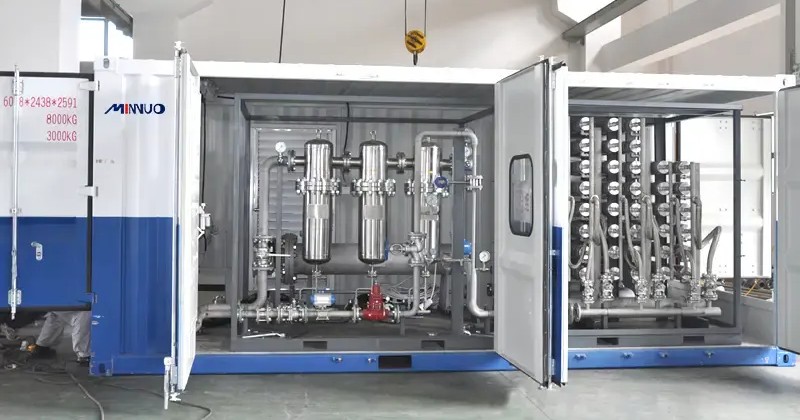
三、高温问题的解决方法
(一)优化设备运行环境
确保设备安装在通风良好、远离热源的区域:
在设备安装选址时,应选择通风良好的开阔空间,避免将设备安装在狭小、封闭的房间内。同时,要确保设备周围至少 1 米范围内没有热源,如高温炉窑、蒸汽管道等。如果无法避免靠近热源,应采取有效的隔热措施,如设置隔热屏障等。
必要时加装散热风扇或空调:
对于一些安装环境温度较高且通风条件有限的场所,可以考虑加装散热风扇或空调来降低设备周围的环境温度。散热风扇可以安装在设备的散热口附近,通过强制对流的方式加速设备内部热量的散发。空调则可以将整个设备安装区域的温度控制在适宜的范围内,为设备的稳定运行创造良好的环境条件。
定期清理设备外壳及散热口灰尘:
设备外壳和散热口上的灰尘会阻碍热量的散发,因此需要定期对其进行清理。可以使用干净的抹布擦拭设备外壳,对于散热口上的灰尘,可以使用压缩空气进行吹扫。建议每周至少进行一次设备外壳的清洁,每月至少进行一次散热口的深度清理。
(二)检查气流系统
检测空压机输出压力是否稳定(建议0.7~1.0MPa):
定期使用气压表检测空压机的输出压力,确保其稳定在建议的压力值在0.7~1.0MPa。根据《GB/T 38624-2020 气体分离设备通用技术规范》,空压机输出压力应稳定在0.7~1.0MPa范围,低于0.6MPa需触发低压报警系统。如果空压机输出压力不足,应及时对空压机进行检查和维修。可能的原因包括空压机的进气过滤器堵塞、活塞磨损、密封件老化等,需要根据具体情况进行清洗、更换等操作。
清洁或更换堵塞的过滤器:
对于管路中的过滤器,应定期进行检查和维护。如果发现过滤器积碳、堵塞严重,应及时进行清洁或更换。清洁过滤器时,可以使用专用的清洗剂浸泡、冲洗,然后用压缩空气吹干。如果过滤器已经损坏或无法通过清洁恢复正常性能,应及时更换新的过滤器。建议每 3 个月对过滤器进行一次检查,根据实际情况决定是否需要清洁或更换。
检查管路接头是否漏气:
仔细检查管路系统中的各个接头,查看是否有漏气现象。可以使用肥皂水涂抹在接头处,观察是否有气泡产生来判断是否漏气。如果发现管路接头漏气,应及时进行修复。对于松动的接头,可以拧紧螺母;对于损坏的密封件,应及时更换新的密封件。
确保气压开关(0.4MPa 阈值)灵敏有效:
定期对气压开关进行测试,检查其在气压达到 0.4MPa 时是否能够正常闭合,以及在气压低于 0.4MPa 时是否能够正常断开。可以通过模拟气压变化的方式来测试气压开关的性能。如果气压开关出现故障,应及时更换新的气压开关,以确保压力联动保护机制的正常运行。
(三)校准温控系统
定期使用标准温度计校准热电偶:
每隔一段时间(建议每半年),使用经过校准的标准温度计对热电偶进行校准。将标准温度计与热电偶放置在同一位置,测量设备内部的同一温度点,然后对比两者的测量结果。如果发现热电偶的测量值与标准温度计的测量值偏差超过允许范围,应及时对热电偶进行调整或更换。每季度使用Class A级热电偶校准仪(如Fluke 1551A),在设备典型工作温度点(20℃、35℃、50℃)进行三点校准,偏差>±1.5%需更换传感器。
调整 PID 参数(比例带、积分时间、微分时间):
根据设备的实际运行情况和温度控制要求,对 PID 温控仪的参数进行优化调整。在调整 PID 参数时,可以采用逐步试凑的方法,先调整比例带,观察温度控制效果,然后再依次调整积分时间和微分时间,直到达到最佳的温度控制精度和稳定性。在调整过程中,要注意记录每次调整的参数值和对应的温度控制效果,以便后续参考。
测试 SSR 继电器通断功能:
定期对 SSR 继电器的通断功能进行测试。可以使用万用表测量继电器的触点电阻,在继电器处于断开状态时,触点电阻应为无穷大;在继电器处于闭合状态时,触点电阻应接近于 0。如果发现继电器的通断功能异常,如触点粘连、无法闭合或断开等,应及时更换新的 SSR 继电器。
(四)调整加热器工作模式
检查加热器额定功率是否与设备匹配:
仔细核对加热器的额定功率是否与膜分离制氮机的设计要求相匹配。如果发现加热器功率过高,应及时更换合适功率的加热器。在更换加热器时,要注意选择质量可靠、符合设备要求的产品,并确保正确安装。
分阶段加热:
通过 PLC 程序设定阶梯升温策略,实现分阶段加热。例如,在设备启动初期,先以较低的功率对设备进行预热,使设备内部温度缓慢上升。当温度达到一定程度后,再逐步提高加热器的功率,使温度快速上升到设定值。这种分阶段加热的方式可以有效减少瞬时热负荷,避免设备因瞬间产生过多热量而导致高温问题。
(五)维护或更换膜组
每半年检测膜组渗透性能:
定期对膜组的渗透性能进行检测。可以通过测量膜组在一定压力和温度条件下,对氧气和氮气的渗透速率来评估膜组的性能。如果发现膜组的渗透性能下降明显,应及时采取相应的措施。
使用专用清洗剂清除污染物:
对于膜组表面和内部的污染物,可以使用专用的清洗剂进行清洗。在清洗膜组时,要严格按照清洗剂的使用说明进行操作,控制好清洗温度、时间和清洗剂的浓度等参数。清洗完成后,要用干净的水对膜组进行充分冲洗,确保膜组内没有残留的清洗剂。
若膜组老化严重(如分离效率下降 30% 以上),需及时更换:
当膜组老化严重,其分离效率下降超过 30% 以上时,即使经过清洗和维护,也难以恢复到正常性能,此时应及时更换新的膜组。在更换膜组时,要选择与原设备型号匹配的膜组,并按照正确的安装步骤进行安装,确保膜组安装牢固、密封良好。

四、预防性维护建议
(一)日常巡检
记录运行温度曲线:
在设备运行过程中,每天定时记录设备的运行温度,并绘制温度曲线。通过观察温度曲线的变化趋势,可以及时发现设备温度的异常波动情况。例如,如果温度曲线呈现持续上升或突然大幅波动的趋势,就可能意味着设备存在潜在的问题,需要进一步排查。
发现异常波动立即排查:
一旦发现设备温度出现异常波动,应立即停止设备运行,并对设备进行全面检查。检查内容包括设备的运行环境、气流系统、温控系统、加热器以及膜组等各个方面,找出导致温度异常波动的原因,并及时采取相应的解决措施。
(二)季度维护
清洁电气触点:
每季度对设备的电气触点进行清洁。电气触点在长期使用过程中,会因为氧化、积尘等原因导致接触电阻增大,影响设备的正常运行。可以使用酒精棉球擦拭电气触点,去除表面的氧化物和灰尘,确保电气触点接触良好。
检查过热保护开关灵敏度:
对过热保护开关的灵敏度进行测试。可以通过模拟设备温度升高的方式,观察过热保护开关是否能够在设定的温度值(≥50℃)时及时动作,切断电源。同时,也要检查过热保护开关在温度下降到设定值(≤35℃)时是否能够正常恢复供电。如果发现过热保护开关的灵敏度异常,应及时进行调整或更换。
(三)年度大修
全面测试温控系统:
每年对膜分离制氮机的温控系统进行一次全面测试。包括对热电偶、PID 温控仪、SSR 继电器以及过热保护装置等各个组件的性能测试。通过全面测试,及时发现温控系统中存在的潜在问题,并进行修复或更换相关组件,确保温控系统的可靠性和稳定性。
更新 PLC 程序逻辑:
随着设备运行时间的增加和生产工艺的变化,原有的 PLC 程序逻辑可能不再完全满足设备的运行需求。因此,每年可以对 PLC 程序进行一次优化和更新,根据设备的实际运行情况和新的控制要求,调整程序逻辑,提高设备的自动化控制水平和运行效率。
优化加热控制算法:
对加热控制算法进行优化,结合设备的运行数据和实际控制效果,调整加热控制策略,进一步提高温度控制的精度和稳定性,降低设备因加热控制不当而导致高温问题的风险。
五、总结
膜分离制氮机的高温问题多由散热不良、控制失灵或部件老化引发。通过精准定位故障源,结合环境优化、系统校准和定期维护,可有效避免膜组损坏,保障设备长期稳定运行。在实际操作中,建议建立设备运行日志,结合智能监控系统实现预测性维护,进一步提升氮气生产效率与安全性。
如果您想从源头解决这些问题,想要购买优质膜制氮设备,请认准MINNUO。